Packaging Innovation
Industry Firsts
At Seneca, packaging innovation comes to fruition when we combine positive environmental and economic forces to address market needs. Some of our most notable firsts have improved the convenience our clients can offer their customers and reduced our ecological footprint:
- First to convert our can making operations to offer cans made without BPA in the lining
- First to introduce vegetables in 4 oz. microwaveable cups
- First to sell shelf stable microwavable vegetables pouches
Efficient Product Packaging
As the only self-made can manufacturer in North America, we use our influence to improve the state of canned packaging. Seneca has successfully implemented down gauging of steel in cans, thermal oxidation and energy recovery on steel sheet coating and use of water-based compounds for coating.
Seneca has been able to reduce the amount of steel used by 10% in the ends we make by necking down our cans when possible, including all of our 300 size cans. We have greatly lowered our volatile organic emissions and natural gas consumption by installing state of the art thermal oxidizers resulting in energy savings of $4.64 per thousand sheets of steel.
Stretch Wrap Reduction
Since 2003, Seneca has drastically reduced the amount of stretch wrap used in packaging to reduce the carbon footprint of our suppliers and our own operations. We continue to actively look to our suppliers to provide us with the most environmentally friendly packaging possible.
Pallets
We have recently entered into a program with CHEP Inc. to reduce our reliance on wooden pallets and minimize the impact to the environment. Using over 757,500 CHEP pallets annually (versus one-way white wood) helps us achieve substantial savings.
In addition, our can plants are using over 88% reusable plastic pallets under our own manufactured cans. When broken, the pallets are reground and used again to make new pallets.
CHEP Annual Savings
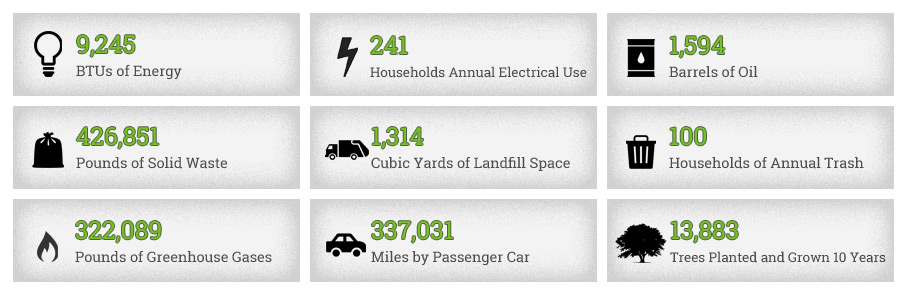